COMPREHENSIVE INDUSTRIAL
WATER TREATMENT SOLUTIONS
Advanced, integrated, end-to-end services and solutions that maximize water recovery and reuse across various industries.
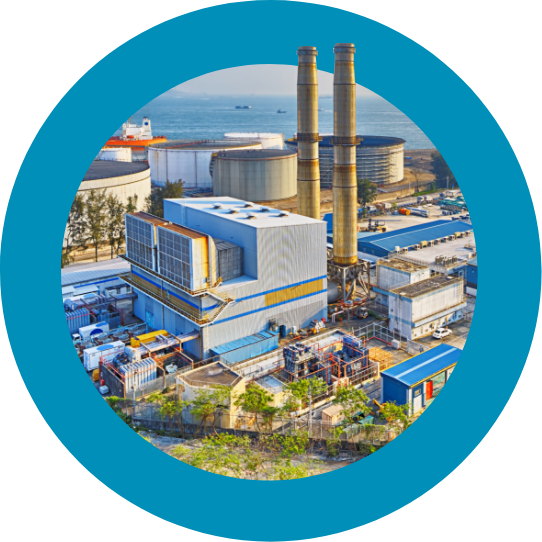
What is Industrial Wastewater Treatment?
There are many uses for water in industry, all of which require treatment either before disposal or for reuse. Our advanced industrial water treatment solutions are successfully deployed worldwide, providing our clients with a one-stop shop and a full process guarantee.
Disposal of industrial wastewater from an industrial plant is a difficult and costly problem. There are many options for disposal, some of which are:
-
Direct Surface Discharge
-
Evaporation Ponds
-
Deep Well Injections
-
Discharge To a Local WWTP
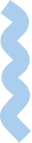
However, all these “solutions” are costly and do not add any value to the plant operation. Therefore, it is important to minimize the effluents for disposal as much as possible, and to recycle and increase reuse of the water back into the process as much as possible.
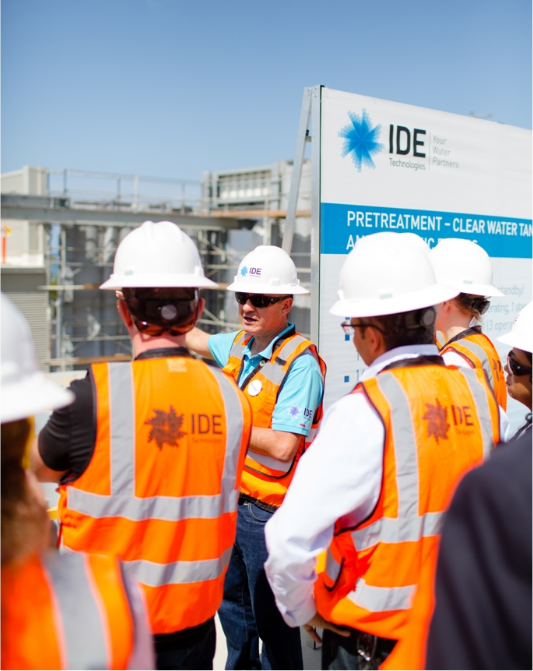
We understand your water needs
For over 60 years we’ve been developing and delivering membrane and thermal based water treatment solutions across the globe. We understand the challenges of treating complex types of water, and our team is ready to address your challenges. We have a full product catalog, and we thrive on tailoring a holistic solution to address the overall need with a comprehensive, integrated, end-to-end approach that guarantees your peace of mind.
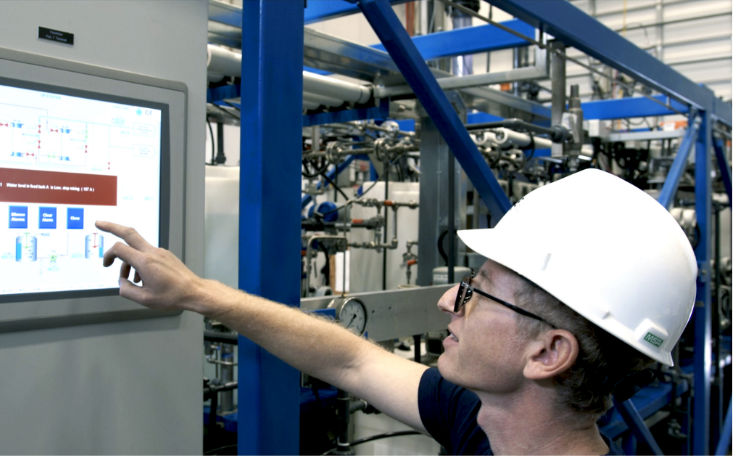
We excel in maximizing recovery
We can treat the toughest wastewater and offer the highest wastewater recovery rates in the industry, utilizing a smart combination of our proprietary MAXH2O products with a wide range of additional water treatment technologies, customized to meet the unique needs of each industry
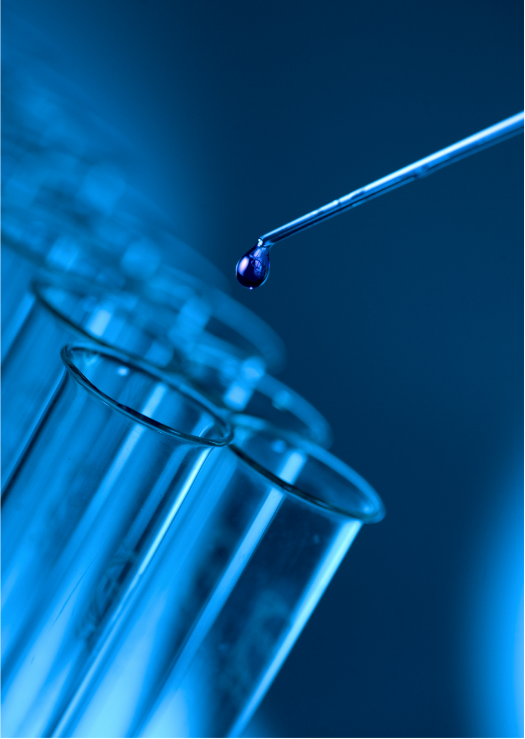
We understand the chemistry of water
IDE Water Technologies fully understands both the chemistry and treatment of wastewater. Our tailored industrial wastewater treatment solutions have been implemented worldwide, and some have been operating for decades. Our solutions help many industries including mining, power, petrochem, chemicals, data centers, microelectronics, semiconductors, and refineries, tackle and overcome their wastewater treatment challenges.
What challenges do industries face today?
One of the greatest challenges facing the water industry is addressing the brine or industrial effluents that are byproducts of core processes in industrial facilities. These effluents are typically characterized by challenging water chemistry, which limits the ability to reach high recoveries due to the risk of scaling and fouling.
While seawater chemistry is well known, and can be treated to a certain extent within the mechanical limitations of the membrane, treating industrial effluents presents a new set of challenges. Industrial effluent generally contains high levels of suspended and dissolved impurities that must be addressed prior to discharge of said effluent.
While membrane technology is also limited by the osmotic pressure limit, when using membranes for industrial water treatment, the limiting factor of water chemistry becomes a challenge way before the osmotic pressure is reached.
Most solutions attempt to tackle the membrane limitation when treating industrial effluents, but addressing the water chemistry is a whole different ballgame, and often overlooked!
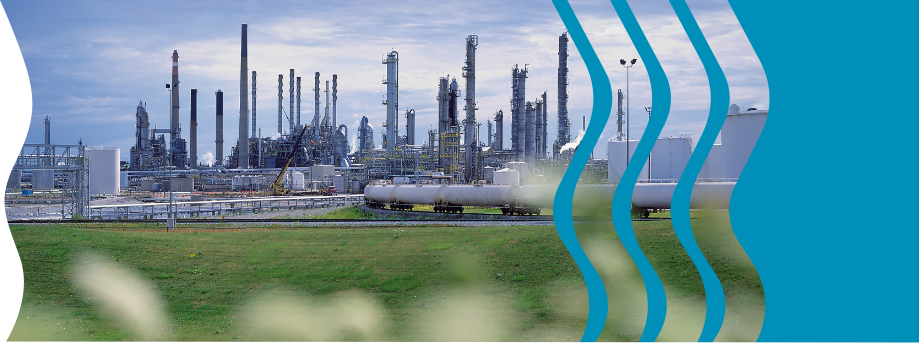
High Recovery Solutions for Industrial Wastewater Treatment
Our game-changing technology solutions and services transform your industrial wastewater treatment challenges into valuable water assets. We have developed economical, sustainable, and reliable thermal and membrane-based water treatment solutions that achieve the industry’s highest recovery rates.
Our innovative brine management solutions, based on our proprietary MAXH2O product line, minimize brine volume, reduce your disposal costs and meet regulatory requirements, and maximize fresh water recovery to help you meet your reuse potential.
MAXH2O Desalter
A Unique RO process that operates at a very high recovery rate without compromising the membranes’ service life.
The patented MAXH2O Desalter maxmizes the potential of RO to treat brine by eliminating the limitation of water chemistry. It operates by recirculating treated water through the RO system at high shear velocity, continuously precipitating supersaturated salts from the recirculated brine.
MAXH2O Pulse Flow RO (PFRO)
An innovative method for operating reverse osmosis water reuse systems that enables operation at high recovery and high flux.
Our proprietary patented Pulse Flow RO (PFRO) technology challenges conventional RO operation by discharging brine in a pulse flow regime withshort forceful surges. The frequently and rapidly changing osmotic and gauge pressure prevents the formation of biofouling and eliminates the need for chloramine dosing.
COOLING TOWER BLOWDOWN TREATMENT - IDE’s end-to-end solutions maximize the overall recovery and minimize the volume for disposal.
Learn MoreOur full range of unique benefits for wastewater treatment:
-
High recovery technologies as an integrated part of our design to reuse and recycle as much of the water as possible.
-
End-to-end water treatment from pre-treatment, through membrane solutions up to ZLD with thermal technologies.
-
Reduced OPEX and CAPEX compared to conventional solutions.
-
Proven track record in EPC, turnkey, O&M, BOT and other business models.
-
Fully customizable to a variety of water sources and customer requirements.
-
Modular design capability with a short set-up time suitable for remote locations.
-
Global delivery
capabilities.
Industrial Wastewater Treatment Solutions
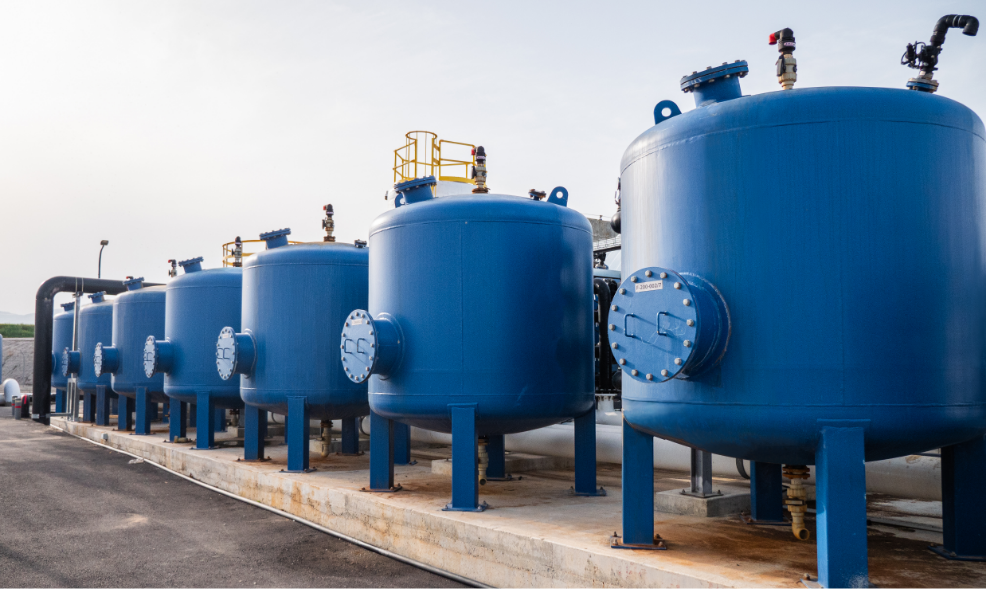
PRE-TREATMENT
Industrial plants in most sectors create wastewater with their processes. This wastewater can be discharged, based on local regulations and permit requirements, or re-used within their process.
The term “pre-treatment” refers to the treatment of wastewater to remove harmful materials before being discharged to a sewer system under the control of a publicly owned wastewater treatment plant.
Learn more about IDE’s complete range of pre-treatment solutions.
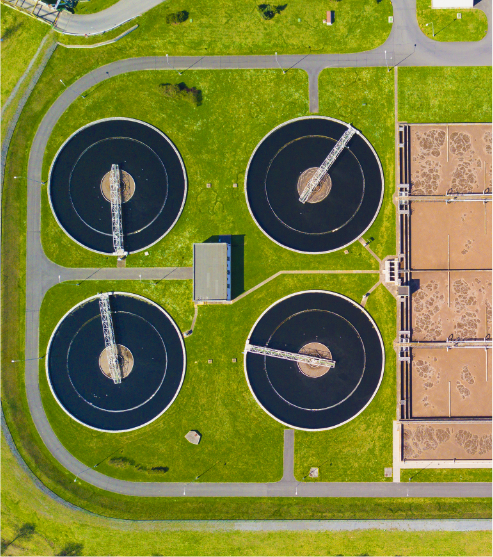
BIOLOGICAL TREATMENT
Biological wastewater treatment is often used as a secondary treatment process to remove material remaining after primary treatment. Biological treatments rely on bacteria, nematodes, or other small organisms to break down organic waste using normal cellular processes.
Find out about IDE’s specialized bio-treatment solutions for various industries.
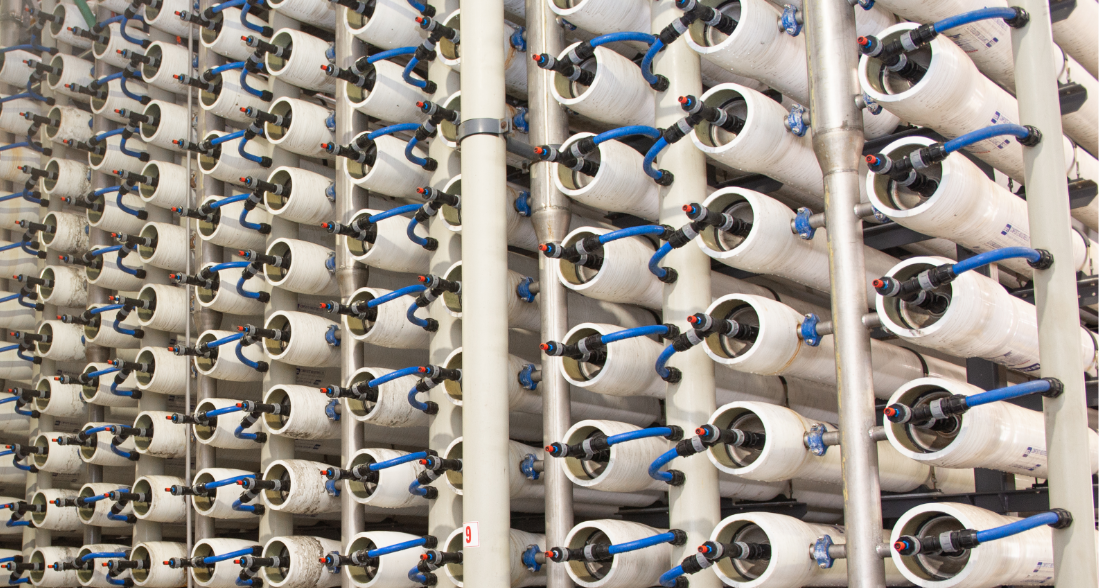
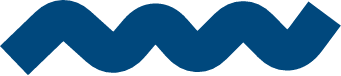
REVERSE OSMOSIS
Reverse Osmosis (RO) uses the principle of osmosis to remove salt and other impurities by transferring water through a series of semi-permeable membranes. As water desalination plants expand globally, they are required to meet sustainable development goals.
Learn how IDE’s solutions alleviate water challenges while minimizing environmental impact and decreasing our customers’ energy and water footprints.

PERMEATE
POLISHING
The RO process removes over 99% of the dissolved solids from the feedwater, leaving approximately 1%, which is unacceptable for many applications. RO permeate is not considered of equal quality to demineralized or deionized water, nor is it considered ultrapure water. To achieve and maintain this level of purity, the RO permeate must be ‘polished.’
Read more about IDE’s two stages of permeate polishing.
ZLD (ZERO-LIQUID DISCHARGE)
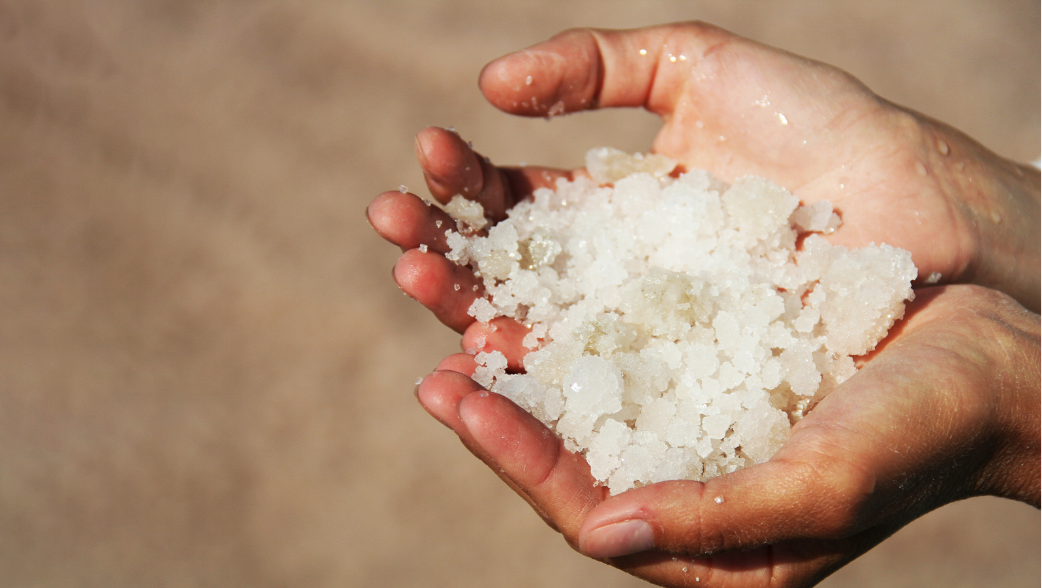
Zero liquid discharge (ZLD) is a water treatment process in which all wastewater is purified and recycled; therefore, leaving zero discharge at the end of the treatment cycle. Zero liquid discharge is an advanced wastewater treatment method that includes ultrafiltration, reverse osmosis, evaporation/crystallization, and fractional electrodeionization.
Zero Liquid Discharge (ZLD) desalination is the ideal solution for brine treatment and wastewater discharge – a complete closed-loop cycle where discharge is eliminated and environmental regulations are met.
Learn how ZLD technology converts a high volume of liquid waste to distilled water for reuse and solidifies salts that can be landfilled or used as raw material for the chemical industry.
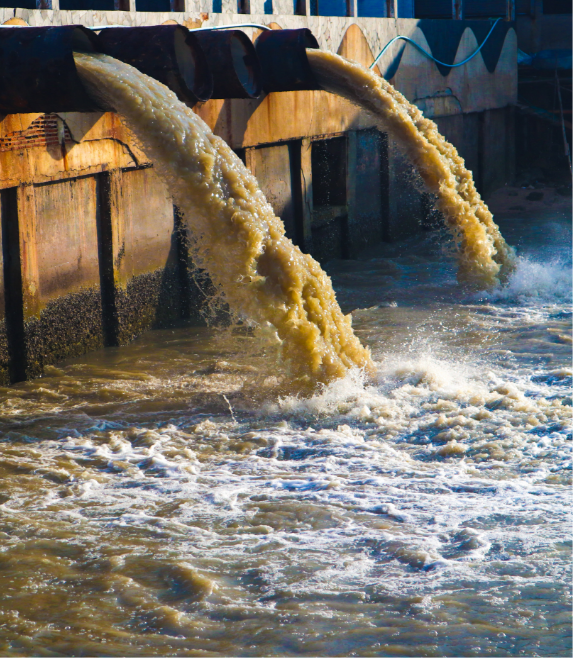
HIGH RECOVERY & BRINE MINIMIZATION
IDE Water technologies has developed two innovative technologies for maximizing recovery and complying with regulatory requirements – MAXH2O Desalter and MAXH2O PFRO.
The MAXH2O Desalter is a state-of-the-art RO solution that includes an integrated salt precipitation cycle for high recovery applications. MAXH2O Desalter process enables pushing the RO water treatment ability to its limit while overcoming the challenging limitation of membrane scaling and fouling – all this while enabling brine minimization and achieving the industry’s highest recovery rates.
MAXH2O PFRO technology overcomes the challenges of conventional RO operation by discharging brine in a pulse flow regime through short, high-velocity surges. The frequently and rapidly changing osmotic and hydraulic conditions reduce biofouling and scaling tendency allowing to push the recovery of the RO to new heights. Additionally, PFRO simplifies the preventive maintenance approach, which increases the time between CIPs and prolongs the life duration of the membranes.
Treat the toughest water by utilizing a smart combination of our proprietary MAXH2O products with a wide range of additional brine minimization and water treatment technologies.
treatment regulations:
Wastewater treatment regulations are becoming ever more stringent, following worldwide recognition of the need to preserve the environment. Regulations are not limited only to the amounts you can discharge, but also address the levels of pollutants that can be discharged.
The Clean Water Act (CWA) establishes the basic structure for regulating discharges of pollutants into the waters of the United States, and regulating quality standards for surface waters. Under the umbrella of the CWA, the US Environmental Protection Agency (EPA) has developed national water quality criteria recommendations for pollutants in surface waters, as well as produced a comprehensive Guide for Industrial Waste Management, with the objective of providing facility managers and regulators with recommendations and tools to better address the management of the large quantities of waste generated by industrial water treatment facilities.
Federal water quality criteria define the maximum permissible levels of various pollutants that will ensure the protection of marine life and human health. Water quality standards are developed to maintain this quality of water, and the responsibility for these standards rests at State level.
The EPA develops national wastewater discharge standards – Effluent Guidelines – on an industry-by-industry basis. These are technology-based regulations and are intended to represent the greatest reductions of pollutants that are economically achievable for an industry.
The standards for direct dischargers are incorporated into National Pollutant Discharge Elimination System (NPDES) permits issued by States and EPA regional offices, and permits, or other control mechanisms for indirect dischargers
Preventing pollution requires a comprehensive, holistic approach; an approach that looks at an entire facility – from its physical design, through its production processes and products, with the aim of identifying how to mitigate and minimize environmental impacts across the facility. The Pollution Prevention Act of 1990, a national, 4-step policy calls for:
- Examination of waste streams and technologies to identify opportunities for recycling and/or reusing wastewater
- Reducing volume and contamination of waste prior to final disposal to reduce costs and comply with regulations
- Minimum amount to authorized sites, MLD or ZLD are high priority
- Any practice that reduces pollution prior to recycling/reusing treatment, and/or disposal. Proper maintenance of filters and membranes
Related Solutions
All solutions

Related Projects
-
Wastewater Treatment for a Semiconductor Manufacturer (Israel)
Semiconductor, PFRO, Wastewater treatment, Water treatment
Read more -
Cherokee Wastewater Treatment Plant (USA)
PFRO, Wastewater Treatment, Municipal
Read more -
Wintershall Oil & Gas Project (Germany)
Desalination, MVC, EPC, Oil & Gas, IWT
Read more -
Koyambedu Wastewater Treatment Plant (India)
Wastewater treatment, RO, Municipal, O&M, DBO, TTRO
Read more